How to Make Silicone Parts: DIY Methods vs Professional LSR Injection Molding?
Introduction
Whether you're developing a prototype or preparing for mass production, choosing the right silicone manufacturing method significantly impacts cost, quality, and lead time. While DIY approaches may work for simple projects, professional-grade silicone parts require precision engineering and advanced techniques like Liquid Silicone Rubber (LSR) Injection Molding.
In this guide, we’ll compare DIY silicone molding with industrial LSR manufacturing—and explain why partnering with an expert like SiliconePlus ensures superior performance, durability, and scalability.
Can You Make Silicone Parts at Home? (DIY Methods & Limitations)
Many hobbyists and startups experiment with silicone casting (room-temperature vulcanizing, or RTV silicone) for simple shapes. While this method is low-cost, it has critical drawbacks:
Poor Precision (±1mm tolerance vs. ±0.05mm in LSR molding).
Low Durability – Prone to tearing, UV degradation, and heat failure.
Limited Scalability – Hand-poured molds can’t match automated production speeds.
Example: A hand-cast silicone wristband may last 6 months, while an LSR-injected strap endures years of sweat, sunlight, and stretching.
When to Go Pro?
If your project requires:
✔ Medical/food-grade compliance (FDA, ISO 10993)
✔ Complex geometries (thin walls, undercuts)
✔ High-volume production (10,000+ parts)
—LSR injection molding is the only viable solution.
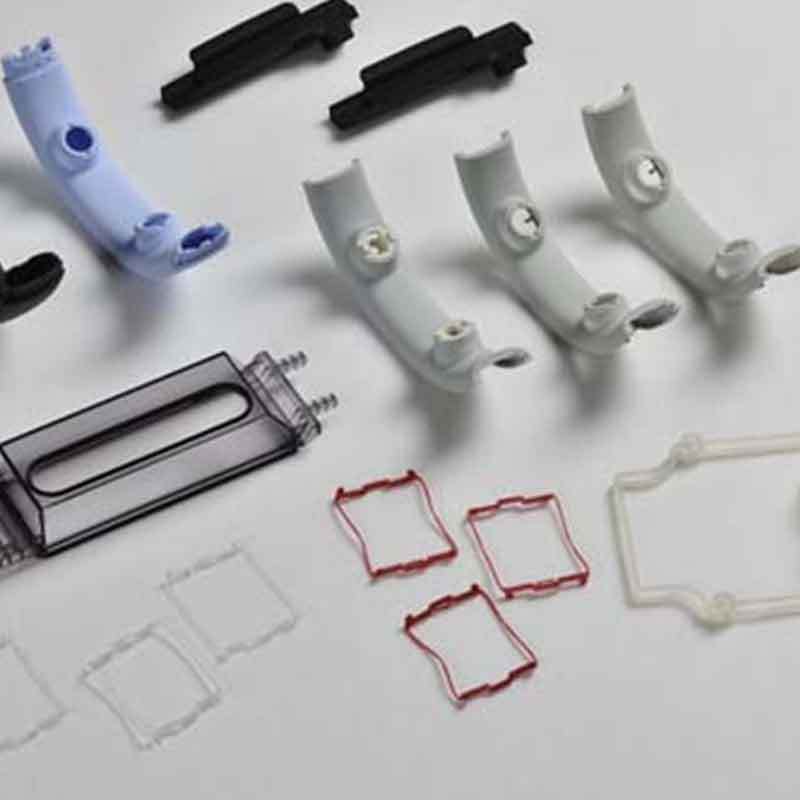
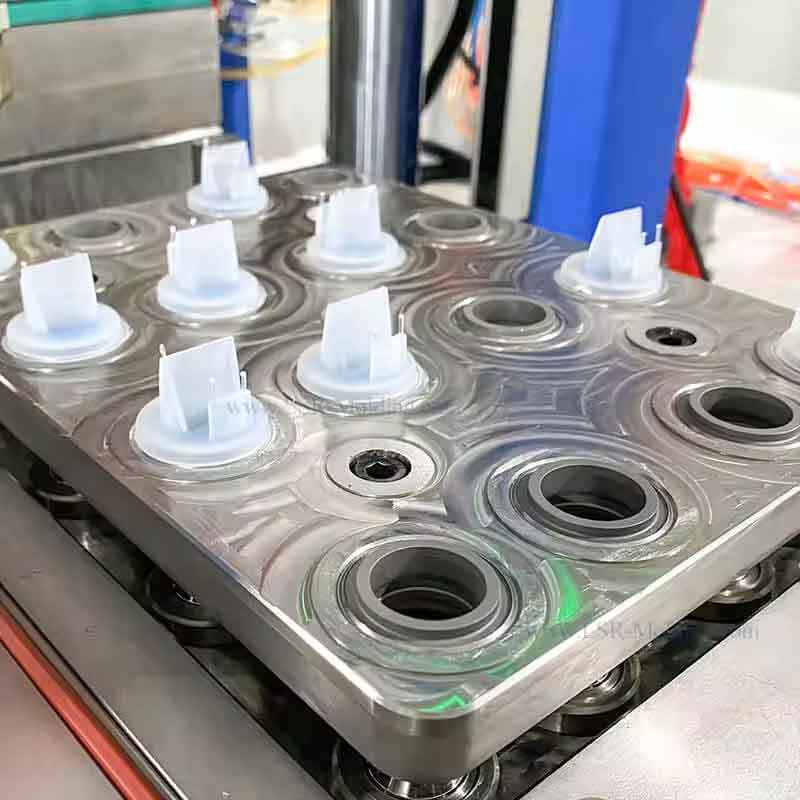
How SiliconePlus Makes High-Performance Silicone Parts
As a leading custom silicone parts manufacturer, we combine material science, precision tooling, and automated LSR injection to deliver:
Step 1: Material Selection
Medical-Grade LSR (FDA, USP Class VI) for implants/wearables.
Thermally Conductive silicones for electronics.
Shore Hardness 10A-80A (ultra-soft to rigid).
Step 2: Mold Design & Tooling
Hardened steel molds (50K+ cycles lifespan).
Multi-cavity molds to reduce per-unit costs.
3D-printed prototypes for design validation.
Step 3: LSR Injection Process
Fully automated presses with ±0.02mm repeatability.
Flashless molding for zero post-processing.
Overmolding (e.g., silicone + plastic/glass).
Step 4: Quality Assurance
100% dimensional inspection (CMM machines).
Tensile/tear testing per ASTM D412.
Sterilization validation (autoclave, ETO, gamma).
Why Choose SiliconePlus for Your Project?
✅ 72-Hour Prototypes – Fast-track your R&D.
✅ ISO 13485 & ISO 9001 Certified – Medical/industrial compliance guaranteed.
✅ End-to-End Support – From DFM analysis to logistics.
Free Design Review Offer:
Submit your CAD file for a free manufacturability audit and quote within 24 hours.
FAQ
Q: How much does a custom silicone mold cost?
A: From 2,000 (simple designs) to2,000(simpledesigns)to20,000+ (multi-cavity, micro-features).
Q: Can you match Pantone colors?
A: Yes – We support custom pigments and translucent/opaque finishes.
Q: What’s the MOQ for LSR parts?
A: As low as 500 pieces for production runs.