How to Mold Silicone Rubber: Techniques and Applications
Silicone rubber has become essential across industries due to its unique properties, like durability, flexibility, and resistance to extreme temperatures. At Siliconeplus, we are dedicated to empowering our clients' products by incorporating silicone overmolding, silicone molding, and liquid injection molding techniques. Through our expertise, we help clients achieve exceptional performance in their fields. In this article, we’ll explore how to mold silicone rubber, the processes involved, and the unique advantages of each method.
Why Mold Silicone Rubber?
Silicone rubber is versatile, biocompatible, and offers high resilience in challenging environments. Whether used alone or combined with materials like metal, plastic, or flexible printed circuits (FPC), molded silicone can enhance product functionality, durability, and user experience. This versatility makes silicone molding techniques highly valuable across industries, from medical and automotive to electronics and consumer goods.
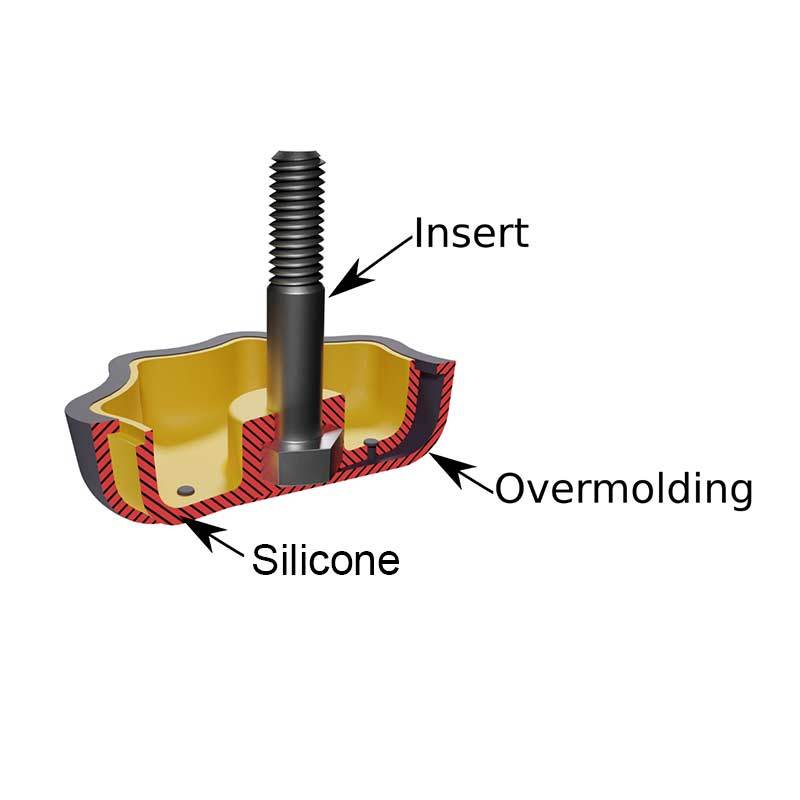
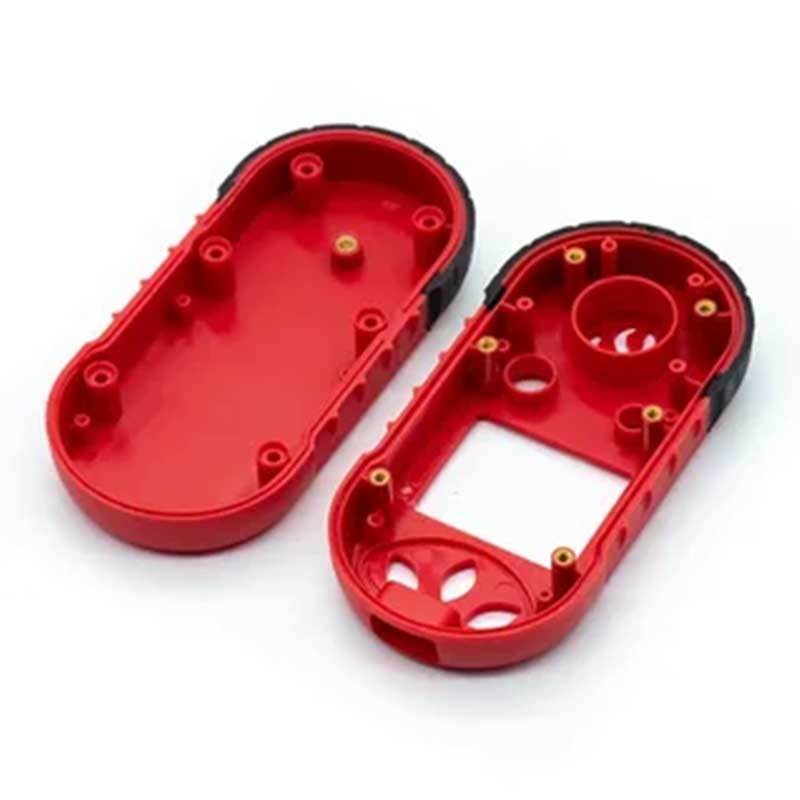
Silicone Molding Techniques
To create high-quality, custom silicone products, Siliconeplus employs various silicone molding techniques tailored to different applications and performance requirements.
1. Silicone Overmolding
Silicone overmolding is a process where silicone is molded over a substrate material, such as metal or plastic, to form a unified component. This technique is ideal for applications that require a strong bond between silicone and another material. Overmolding adds functional benefits like improved grip, shock absorption, and waterproofing.
At Siliconeplus, we utilize overmolding to provide custom solutions that are not only durable but also enhance product aesthetics and user comfort. For example, in electronics, silicone overmolding protects sensitive components, while in automotive applications, it provides a non-slip, comfortable grip on handles and buttons.
2. Liquid Injection Molding (LIM)
Liquid Injection Molding (LIM) is a high-precision process that involves injecting liquid silicone rubber (LSR) into a mold. This method is highly efficient, enabling large-scale production of complex parts with tight tolerances. LIM is widely used in industries where biocompatibility, heat resistance, and flexibility are critical.
At Siliconeplus, our liquid injection molding process is streamlined to achieve consistent, high-quality parts for various applications. This technique is particularly beneficial for medical devices, baby products, and food-grade components, where safety and quality are essential.
3. Compression Molding
Compression molding is one of the oldest and most reliable silicone molding techniques. In this process, pre-heated silicone material is placed in a heated mold, and pressure is applied to shape it precisely. This method is ideal for producing large or thick parts that require uniform consistency.
Siliconeplus uses compression molding to produce custom silicone components that meet specific industry needs. Our team leverages this method to deliver robust, high-performance parts for clients in industries ranging from industrial equipment to consumer goods, where durability and reliability are key.
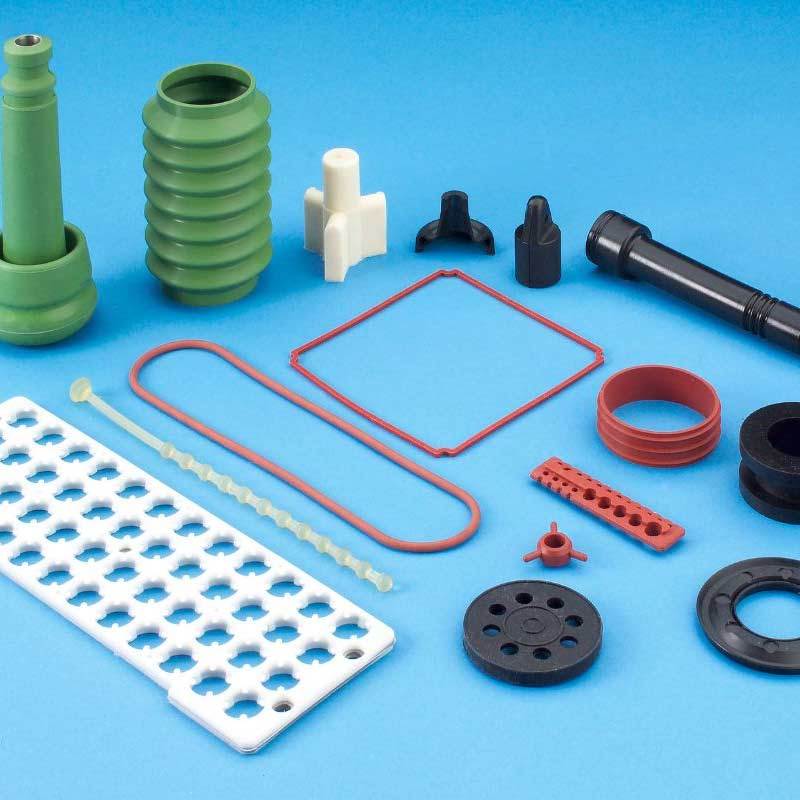
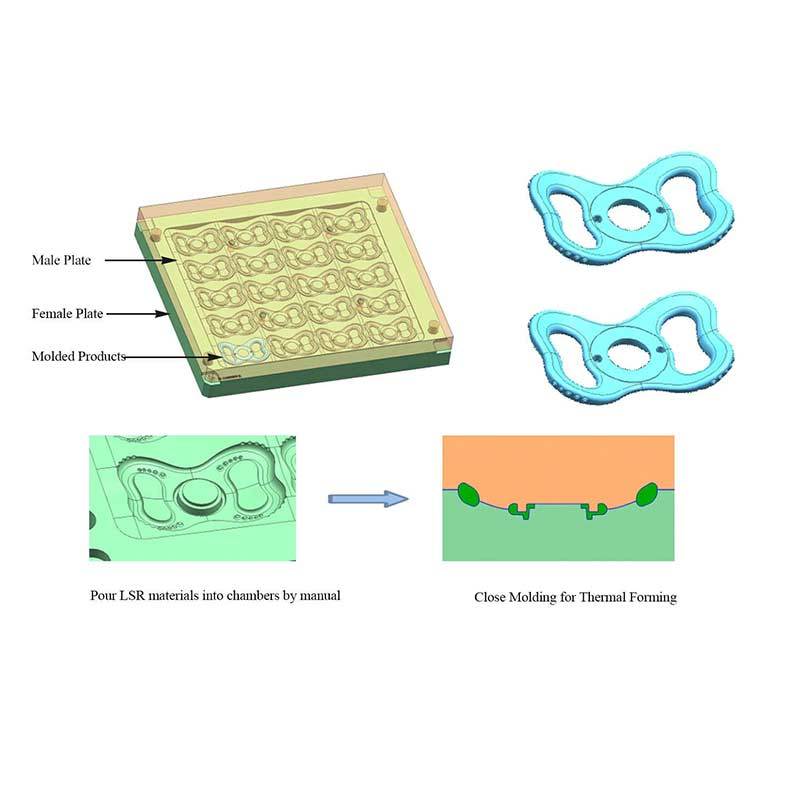