Silicone Mold vs. Injection Mold: Which One is Better for Your Product?
When choosing a manufacturing process for your product, silicone molding and injection molding are two popular options. But which one is better? The answer depends on your product’s material, application, durability requirements, and production scale. At Siliconeplus, we specialize in silicone overmolding and understand how to optimize each process to meet industry demands.
In this article, we’ll compare silicone molding and injection molding in terms of material compatibility, flexibility, cost, and performance, helping you make an informed decision.
What is Silicone Molding?
Silicone molding refers to the process of shaping liquid silicone rubber (LSR) or solid silicone rubber (HCR) into a specific form. It includes techniques like liquid silicone overmolding and compression molding, which are widely used in medical, automotive, electronics, and consumer goods industries.
✅ Advantages of Silicone Molding:
✔ High flexibility – Perfect for soft-touch applications.
✔ Extreme temperature resistance – Withstands -60°C to 250°C, ideal for medical and automotive use.
✔ Biocompatibility – Safe for medical implants, baby products, and food-contact items.
✔ Superior sealing properties – Waterproof, dustproof, and chemical-resistant.
✔ Overmolding compatibility – Bonds with plastic, metal, and electronic components.
🚀 Best Applications:
Medical devices (breathing masks, catheters)
Automotive seals & gaskets
Waterproof electronics components
Wearable technology
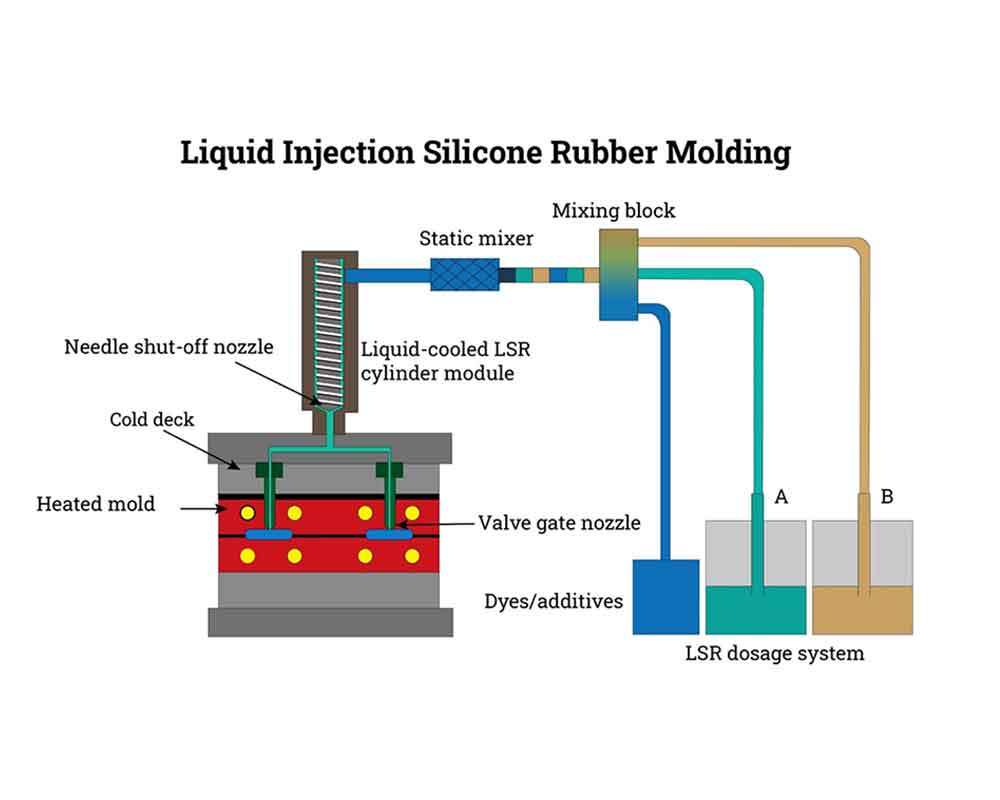
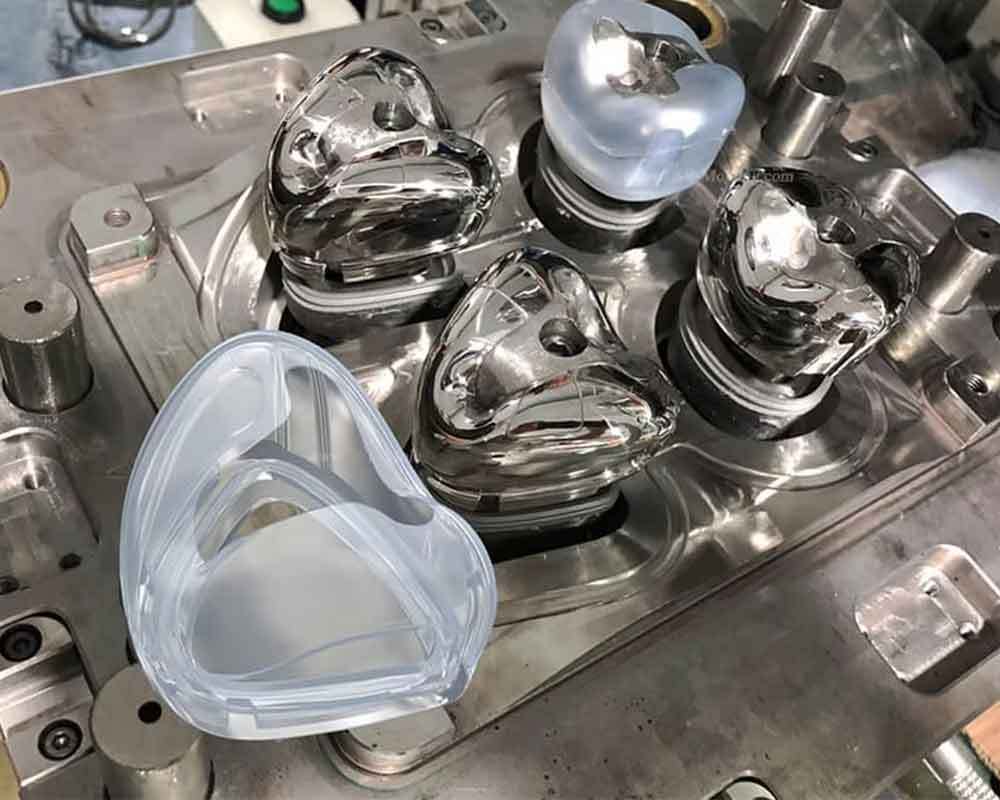
What is Injection Molding?
Injection molding is a process where plastic materials (like ABS, PP, PC) are melted and injected into a mold cavity. It is widely used for mass production in industries like automotive, electronics, and packaging.
✅ Advantages of Injection Molding:
✔ High-speed production – Ideal for large-scale manufacturing.
✔ Cost-effective for mass production – Low per-unit cost after initial mold investment.
✔ Consistent quality – Produces identical parts with tight tolerances.
✔ Variety of material choices – Works with plastics like ABS, nylon, PC, and PP.
🚀 Best Applications:
Plastic casings (electronics, automotive parts)
Packaging (bottle caps, containers)
Household items (toys, utensils)
High-volume production of rigid parts
Silicone Molding vs. Injection Molding: Key Differences
Feature | Silicone Molding | Injection Molding |
Material | Liquid Silicone Rubber (LSR), Solid Silicone Rubber (HCR) | Thermoplastics (ABS, PP, PC, Nylon) |
Flexibility | High (soft & elastic) | Low (rigid & structured) |
Temperature Resistance | -60°C to 250°C | Typically -20°C to 120°C |
Biocompatibility | Excellent (safe for medical & food use) | Limited (may require additional coatings) |
Sealing Performance | Waterproof, chemical-resistant | Requires additional sealing for waterproofing |
Cost | Higher for small batches but cost-effective for long-term | Lower for high-volume production |
Production Speed | Slower but precise | Fast for large-scale production |
Which One is Better?
It depends on your product requirements:
✔ Choose Silicone Molding if you need:
High flexibility and softness (e.g., medical or wearable products)
Extreme temperature resistance (e.g., automotive gaskets)
Waterproof and chemical-resistant properties (e.g., seals and connectors)
Biocompatibility for medical and food-contact products
✔ Choose Injection Molding if you need:
High-volume production at a lower cost
Rigid and structural components
Faster production cycles
💡 For hybrid applications, consider Silicone Overmolding, where liquid silicone rubber (LSR) is molded onto plastic or metal components, creating a strong, durable bond. This is perfect for electronics, automotive, and medical industries.
Siliconeplus: Your Expert in Silicone Overmolding
At Siliconeplus, we specialize in liquid silicone overmolding and custom silicone solutions, helping businesses achieve high-performance, durable, and innovative products. Whether you need LSR overmolding, precision silicone molding, or hybrid solutions, we deliver tailored solutions for automotive, medical, and electronics industries.
Contact us today to find the perfect silicone molding solution for your product!