The Liquid Silicone Transfer Molding (LSTM) process presentation
The Liquid Silicone Transfer Molding (LSTM) process is a manufacturing technique used to create high-precision, high-quality silicone rubber parts. This method combines aspects of traditional transfer molding with the unique properties of liquid silicone rubber (LSR). Here's an overview of the process:

Liquid Silicone Transfer Molding Process:
Preparation of Raw Materials:
Liquid Silicone Rubber (LSR): LSR is a two-part silicone system, consisting of Part A (a base polymer) and Part B (a curing agent or catalyst). These components are mixed in a precise ratio to achieve the desired material properties.
Colorants and Additives: If required, colorants or other additives are mixed with the LSR to achieve specific properties, such as pigmentation or enhanced mechanical characteristics.
Mixing and Metering:The LSR components (Part A and Part B) are accurately mixed using a mixing unit or machine to ensure homogeneity. The mixture is then metered into the transfer pot or chamber.
Mold Preparation:The mold is designed with a cavity that matches the desired shape and specifications of the final product. It is typically preheated to a specific temperature to facilitate the curing process.The mold consists of multiple parts, including the transfer pot, runner system, and cavities.
Transfer Molding:
Loading: The mixed LSR is loaded into the transfer pot or chamber.
Plunger Action: A plunger or piston forces the LSR through the runner system and into the mold cavities. The material is transferred under pressure, ensuring it fills the cavities completely and uniformly.
Curing: The filled mold is held under pressure at a specified temperature for a certain period, allowing the LSR to cure (cross-link) and solidify.
Demolding and Post-Processing:Demolding: Once the curing process is complete, the mold is opened, and the finished silicone parts are ejected or removed.
Trimming and Finishing: Any excess material (flash) is trimmed, and the parts may undergo additional post-processing steps such as inspection, testing, or secondary operations (e.g., overmolding, bonding).
Advantages of Liquid Silicone Transfer Molding:
High Precision and Quality:
The process allows for the production of complex and detailed parts with tight tolerances.LSR materials provide excellent consistency and quality, resulting in parts with uniform properties.
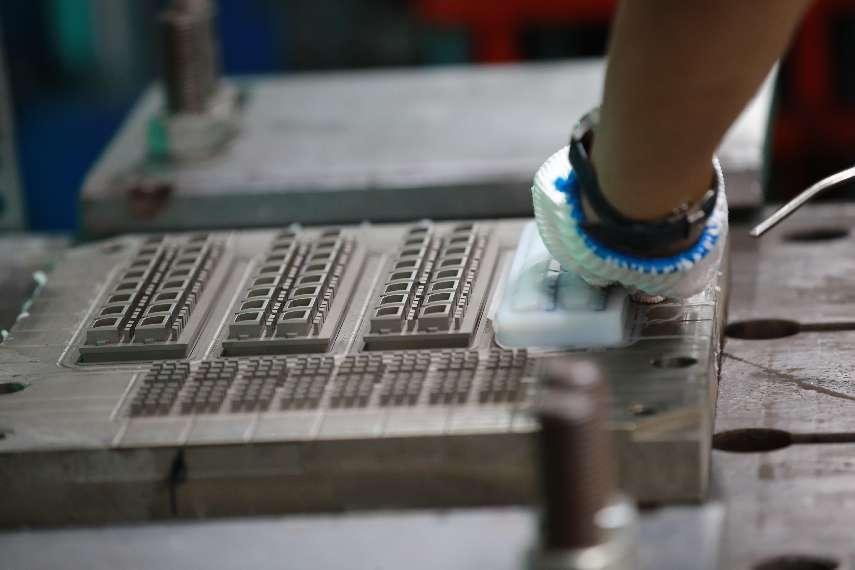
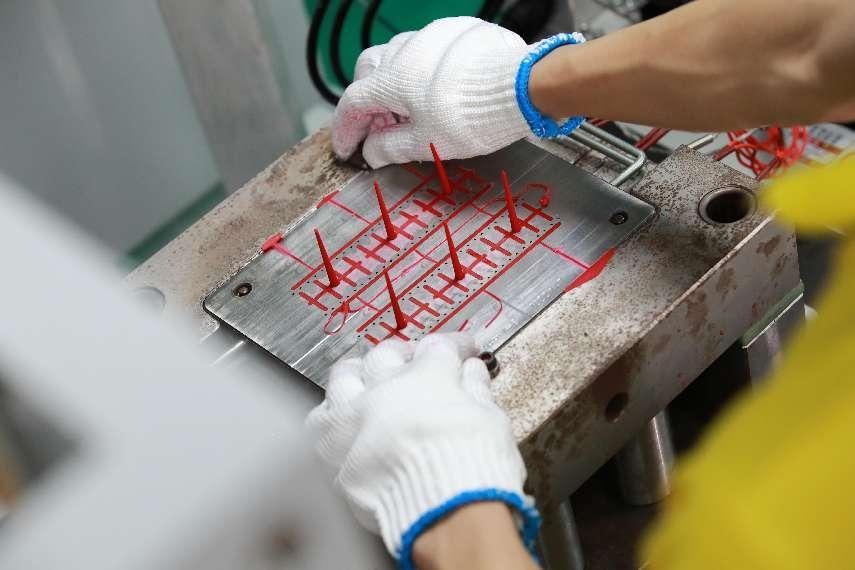
Efficient Production:The automated mixing and metering of LSR ensure precise control over material ratios and reduce material waste.The process is suitable for high-volume production, offering repeatability and reliability.
Material Benefits:LSR has excellent thermal stability, chemical resistance, and biocompatibility, making it ideal for applications in medical devices, automotive components, and consumer products.The material properties of LSR allow for flexibility, durability, and resistance to extreme environmental conditions.
Versatility:The LSTM process can accommodate a wide range of part sizes, shapes, and complexities.It is suitable for producing parts with intricate geometries, fine details, and thin walls.
Applications of Liquid Silicone Transfer Molding:Medical Devices: Seals, gaskets, membranes, and other components requiring biocompatibility and high purity.
Automotive Components: O-rings, gaskets, connectors, and other parts exposed to harsh environmental conditions.
Areas of application
Applications of Liquid Silicone Transfer Molding:Medical Devices: Seals, gaskets, membranes, and other components requiring biocompatibility and high purity.
Automotive Components: O-rings, gaskets, connectors, and other parts exposed to harsh environmental conditions.
Consumer Products: Keypads, kitchenware, baby products, and wearable devices.
Electrical and Electronic Components: Insulators, connectors, and protective covers.
The Liquid Silicone Transfer Molding process is a versatile and efficient method for producing high-quality silicone rubber parts, offering numerous advantages in terms of precision, material properties, and production efficiency.