The difference between silicone secondary injection molding and two-color injection molding?
Silicone secondary injection molding and two-color injection molding are two distinct manufacturing processes used to create multi-material or multi-colored parts.
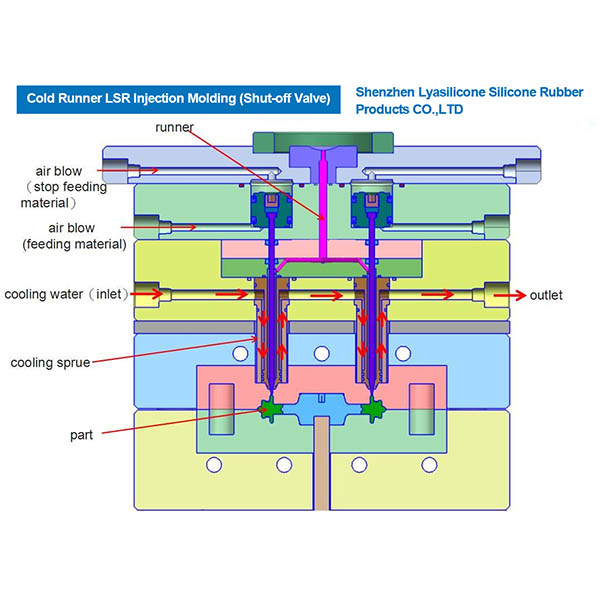
Here are the key differences between the two:
Definition:Silicone secondary injection molding involves injecting liquid silicone rubber (LSR) onto or around a previously molded thermoplastic or another material part. This process is typically used to overmold silicone onto a substrate, creating a product with combined properties of both materials.
Process:
First Stage: The primary part (usually made of thermoplastic) is molded using traditional injection molding techniques.
Second Stage: The molded part is placed into a second mold where LSR is injected over or around it, bonding with the primary material.
Applications:
Medical devices where soft-touch silicone is overmolded onto rigid plastic components.
Consumer products like toothbrushes or kitchen utensils where a soft, grippy silicone surface is required.
Electronics where silicone is used for sealing or insulating parts.
Advantages:Combines the properties of two materials, such as the rigidity of thermoplastics with the flexibility and biocompatibility of silicone.Enhances the functionality and usability of products by adding features like grip, sealing, or cushioning.Provides strong bonding between the two materials.
Two-color injection molding, also known as multi-shot or multi-material molding, involves injecting two different thermoplastic materials into the same mold in a single molding cycle to create parts with two distinct colors or materials.
Process:
First Injection: The first material is injected into the mold to form part of the final product.
Mold Rotation or Transfer: The mold then rotates, or the part is transferred to a second cavity within the same mold.
Second Injection: The second material is injected into the mold, bonding with the first material to complete the part.
Applications:
Automotive parts with different colors or textures for aesthetic and functional purposes.
Consumer electronics where different materials are needed for functional or design reasons, such as hard plastic with soft touch areas.
Toys and household items where multiple colors or materials enhance the appeal and functionality.
Advantages:Produces parts with multiple colors or materials in a single molding cycle, reducing assembly time and costs.Enhances the design and aesthetics of the product.Provides the ability to integrate different material properties, such as hardness and softness, within the same part.

Key Differences
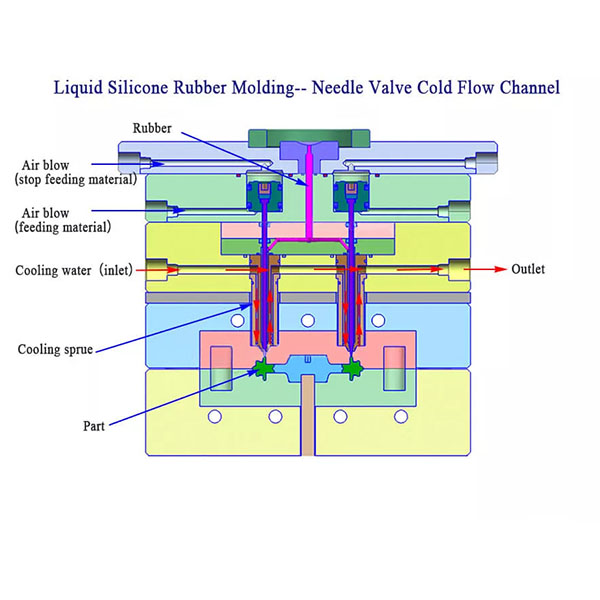
Materials Used:
Silicone Secondary Injection Molding: Combines LSR with another substrate material (often thermoplastic).
Two-Color Injection Molding: Uses two different thermoplastics.
Bonding Method:
Silicone Secondary Injection Molding: Bonds silicone to another material through overmolding.
Two-Color Injection Molding: Bonds two thermoplastic materials within the same mold cycle.
Applications:
Silicone Secondary Injection Molding: Typically used for applications requiring the unique properties of silicone combined with other materials.
Two-Color Injection Molding: Used for parts needing distinct colors or materials for functional or aesthetic purposes.
Process Complexity:
Silicone Secondary Injection Molding: Involves two separate molding stages and potentially different molds.
Two-Color Injection Molding: Performed in a single molding cycle, often with a rotating or transferring mold mechanism.
By understanding these differences, manufacturers can choose the appropriate method based on the specific requirements of their products, whether they need the unique properties of silicone combined with other materials or the integration of multiple colors or materials in a single part.