Understanding the Silicone Injection Molding Process: Key Steps for Custom Solutions
1. Material Preparation
The process begins with the preparation of liquid silicone rubber (LSR), a key component due to its flexibility, heat resistance, and durability. The LSR is a two-part mixture (A and B components), typically stored separately to avoid premature curing. These parts are mixed in precise ratios, ensuring that the silicone reaches the ideal consistency for injection molding.
2. Mold Design and Tooling
The next step involves designing the mold. Silicone injection molding requires highly accurate molds, which are typically made from steel or aluminum, depending on the project specifications. At Siliconeplus, our expert engineering team designs and creates molds that match the client's exact specifications, ensuring precision for complex shapes and customized features.
3. Injection and Curing
Once the mold is ready, the silicone injection molding process begins. The mixed silicone is injected into the mold cavities at high pressure using advanced injection molding machines. During this step, the mold is heated, which initiates the curing process—a critical phase where the silicone solidifies and takes on the desired shape.
4. Cooling and Demolding
After the silicone has fully cured, the mold is allowed to cool. This step ensures the material sets properly before being removed from the mold. Demolding is performed carefully to avoid damaging the finished product, ensuring high precision and a smooth surface finish.
5. Post-Processing
Once the parts are demolded, they may undergo post-processing such as trimming, surface treatments, or additional assembly if needed. Siliconeplus ensures that every product meets the highest quality standards, whether it's combining silicone with metal, plastic, or FPC for unique applications.
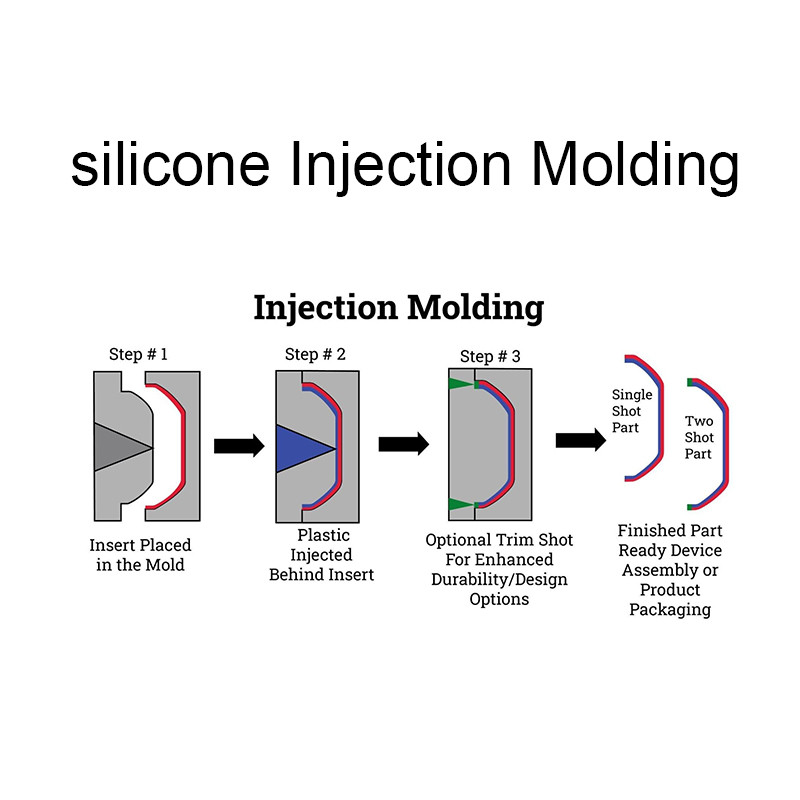
6. Quality Control and Testing
Finally, every silicone product undergoes strict quality control tests. We verify that the product meets performance criteria such as durability, heat resistance, and flexibility. Our extensive quality assurance process ensures that our custom silicone solutions are optimized for specific client needs.
Why Choose Siliconeplus for Your Silicone Injection Molding Needs?
At Siliconeplus, we excel in delivering high-performance silicone products through advanced silicone injection molding. Our expertise allows us to combine silicone with other materials like metal and plastic, offering solutions that meet even the most stringent industry requirements. Whether you're looking for custom parts for industrial applications or medical-grade products, we provide tailored solutions that enhance functionality and innovation.
The silicone injection molding process is ideal for manufacturing complex, high-quality products that meet diverse client demands. By understanding and mastering each step of the process, Siliconeplus is uniquely positioned to offer customized silicone solutions that cater to your specific product needs, whether in electronics, automotive, or medical devices.
Let Siliconeplus help you take your products to the next level with our cutting-edge silicone injection molding process and expert custom solutions.
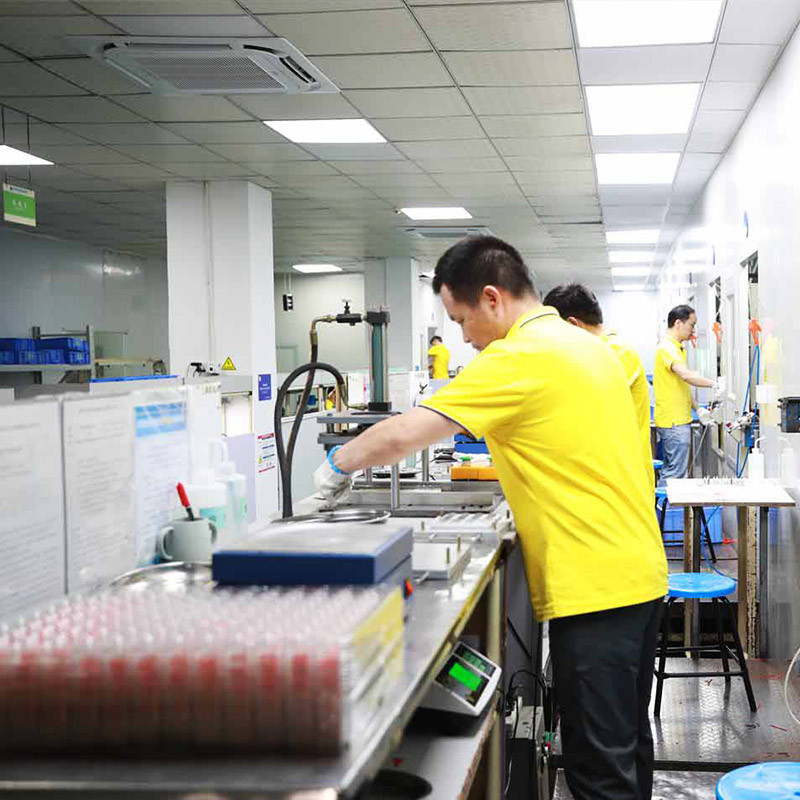