What Materials Can Liquid Silicone Wrap?
Liquid silicone rubber (LSR) is a highly versatile material known for its flexibility, durability, and strong bonding properties with various substrates. When used in liquid silicone molding or silicone overmolding, LSR can effectively wrap around different materials, providing benefits like waterproofing, insulation, shock absorption, and enhanced grip.
Here are some common materials that liquid silicone can wrap, making it ideal for a variety of applications across industries:
1. Metals
Liquid silicone molding bonds exceptionally well with metals like aluminum, stainless steel, and brass. This process is widely used in applications where added grip, insulation, or protection is needed, such as in automotive components, tool handles, and consumer electronics housings. Silicone’s flexibility and durability enhance these metal parts, making them more resilient and user-friendly.
2. Plastics
Various types of plastics, including ABS, polycarbonate, and nylon, are compatible with liquid silicone molding. By wrapping these plastics with LSR, products gain improved durability, shock resistance, and flexibility. This combination is popular in medical devices, consumer electronics, and automotive parts that require a soft-touch layer or protective coating.
3. Glass
Glass components benefit greatly from liquid silicone molding as silicone provides a tight, durable seal, essential in applications such as medical syringes, food storage containers, and laboratory equipment. Silicone’s non-reactive, biocompatible nature is ideal for sealing glass surfaces in products that require cleanliness and airtight properties.
4. Ceramics
In industrial applications, liquid silicone molding provides shock absorption and temperature resistance when wrapped around ceramic parts. This is valuable for products like insulators and specialized equipment that operate in harsh environments, adding an extra layer of protection and longevity to ceramic components.
5. Textiles
Liquid silicone molding can also be used with fabrics and woven textiles, adding durability, water resistance, and flexibility. This makes it highly suitable for products like outdoor gear, footwear, and medical wearables. LSR provides enhanced durability and comfort, protecting fabrics from environmental exposure while maintaining flexibility.
6. Flexible Printed Circuits (FPCs)
In the electronics industry, liquid silicone molding is often applied to encapsulate flexible printed circuits (FPCs). This process protects electronic components from moisture, dust, and mechanical damage, extending their operational lifespan. By providing insulation and flexibility, LSR is an ideal solution for delicate electronics that require both protection and flexibility.
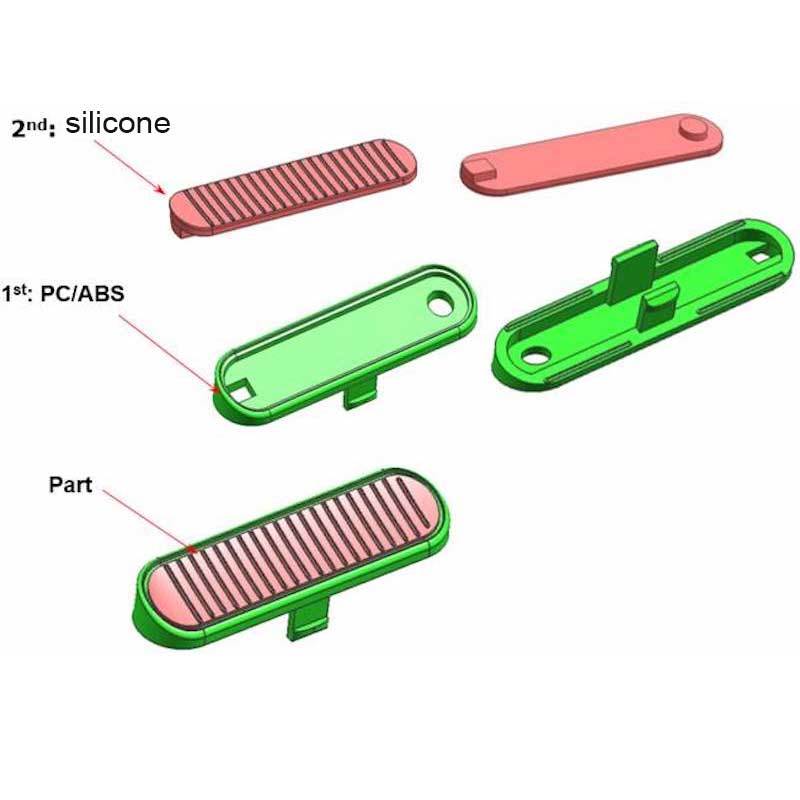
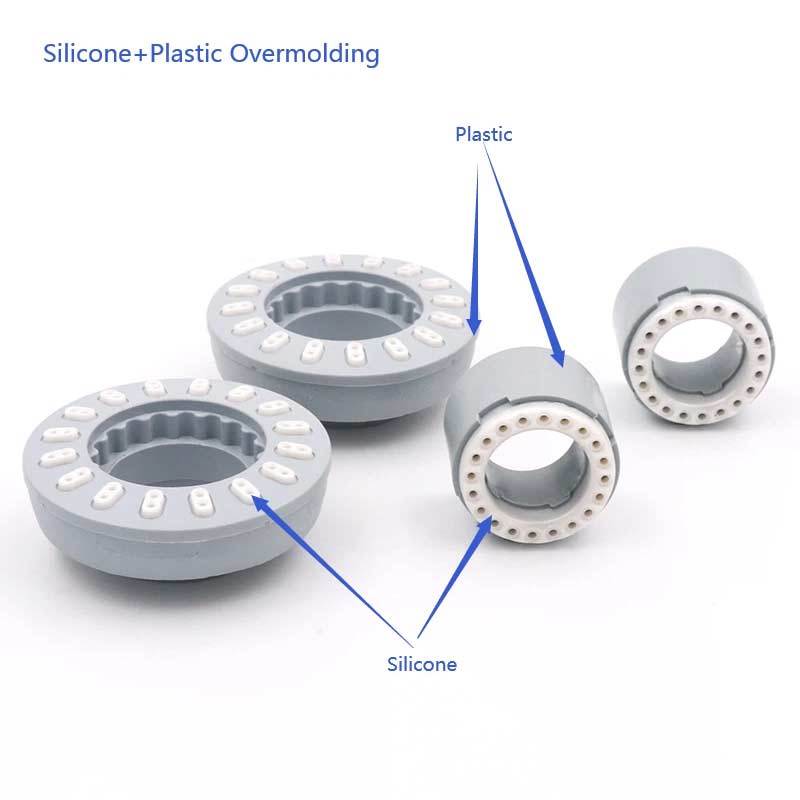
Benefits of Liquid Silicone Molding for Wrapping Different Materials
Enhanced Durability: Liquid silicone molding offers improved resistance to wear, tear, and environmental factors, increasing product longevity.
Waterproofing and Insulation: LSR’s water-resistant and insulating properties make it ideal for applications exposed to moisture, electricity, or extreme temperatures.
Improved Grip and Comfort: Silicone’s flexibility and non-slip properties enhance usability, especially in handles, grips, and consumer goods.
Liquid silicone molding, applied across industries from healthcare to electronics and automotive, provides an efficient solution to improve material performance, protect sensitive components, and enhance the user experience. By choosing Siliconeplus for custom liquid silicone molding services, clients can benefit from industry-leading expertise that empowers their products with silicone’s unmatched durability and adaptability.

