What are the common technical difficulties in the development of silicone products?
1、 Production process control
Temperature, pressure, and time parameter control: The production process of silicone requires strict control of these parameters to ensure product quality and stable performance. For example, during the hot pressing process, the curing temperature range of silicone is narrow, and high or low temperatures can affect the curing effect of silicone, resulting in poor performance of the finished product. Meanwhile, the magnitude and uniformity of pressure also have a significant impact on the shape and quality of the finished product.
Accuracy control: Due to the enhanced fluidity of silicone at high temperatures, the accuracy of the mold is crucial for the quality of the finished product. If the precision of the mold is insufficient, the flow of silicone in the mold will become uneven, which will affect the shape and quality of the finished product.
2、 Raw material selection and quality control
Raw material performance selection: The selection of silicone raw materials directly affects the performance and cost of the product. Different types of silicone raw materials have different physical and chemical properties, which need to be selected according to specific application scenarios. For example, in the medical field, silicone products need to have non-toxic, odorless, and environmentally friendly characteristics, which requires that the raw materials must comply with relevant medical standards.
Stability of raw material quality: The stability of raw material quality is one of the important factors affecting the difficulty of silicone technology. If the quality of raw materials is unstable, it will cause fluctuations in product performance, thereby affecting the reliability and service life of the product.
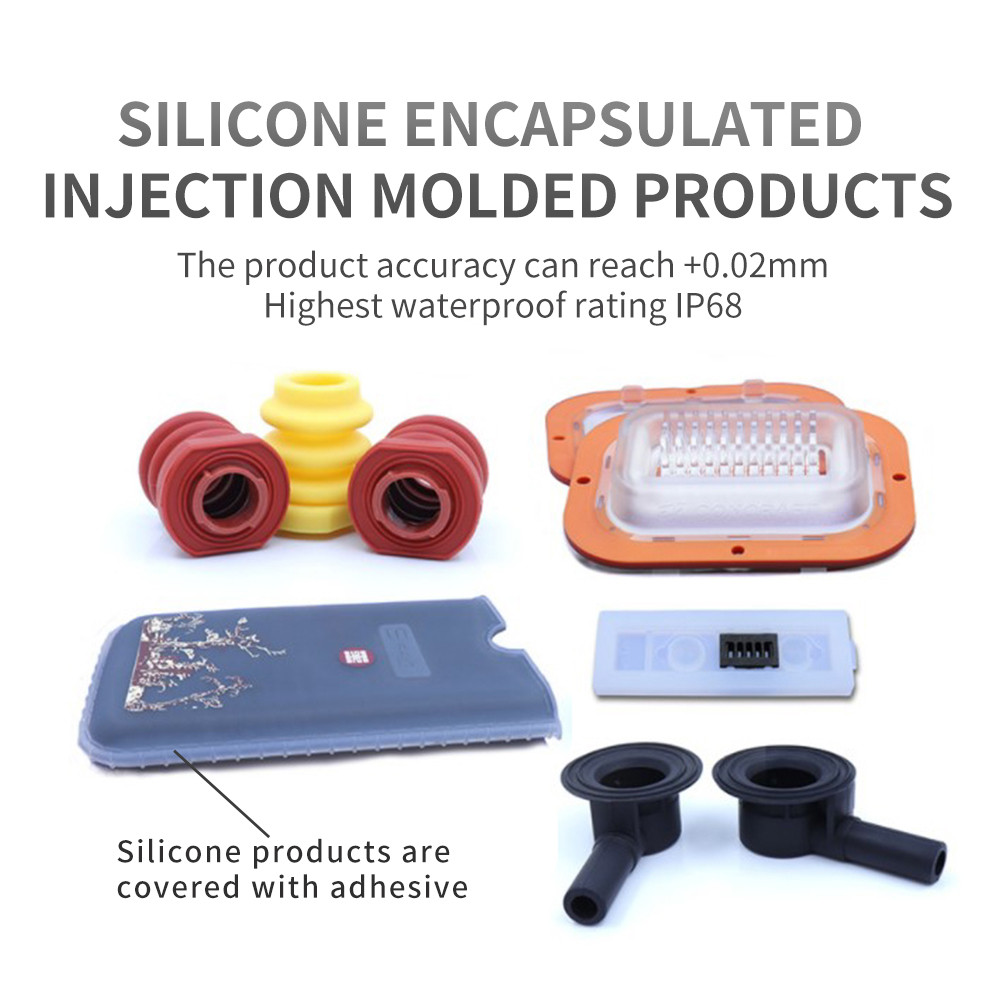
3、 Difficulty in Forming and Processing
Mold design and manufacturing: The molding process of silicone materials involves multiple stages such as mold design and molding technology. The design of the mold must fully consider the fluidity and filling properties of silicone to ensure that the silicone can completely fill the mold and achieve the desired shape. At the same time, the manufacturing of molds also needs to meet high-precision standards.
Bubbles and deformation issues: The viscosity and fluidity of silicone make it prone to problems such as bubbles and deformation during the molding process. For example, in the process of liquid forming, due to the low viscosity and strong fluidity of silicone raw materials, problems such as glue running and bubbles are prone to occur during the injection into the mold. These issues not only affect the shape and quality of the finished product, but may also lead to damage to the mold.
4、 Product Design Challenge
Product curing issue: Incomplete product curing is a common problem, which may be caused by low temperature, insufficient vulcanization time, contamination of the injection pipeline or mold, uneven mixing, low temperature of the rubber material or embedded material. In addition, surface unfamiliarity or partial unfamiliarity of the product is also a major problem, which may be due to improper selection of release agents, mold surface contamination, and contamination of embedded objects.
Reasonable product structure: Due to the fact that the shrinkage rate of silicone is usually greater than that of embedded objects (such as plastic/hardware), the structure of the silicone part of the encapsulated product should be as uniform as possible to avoid local thickness or thinness. At the same time, embedded objects need to have stable positioning within the mold to withstand a certain amount of mold pressure, so the force bearing parts must be balanced. These all need to be fully evaluated and optimized during the product design phase.
In summary, there are various common technical difficulties in the development process of silicone products, from raw material selection to production process control, to molding processing and product design, each link is full of challenges. Corresponding strategies and measures need to be taken to address and optimize these difficulties.
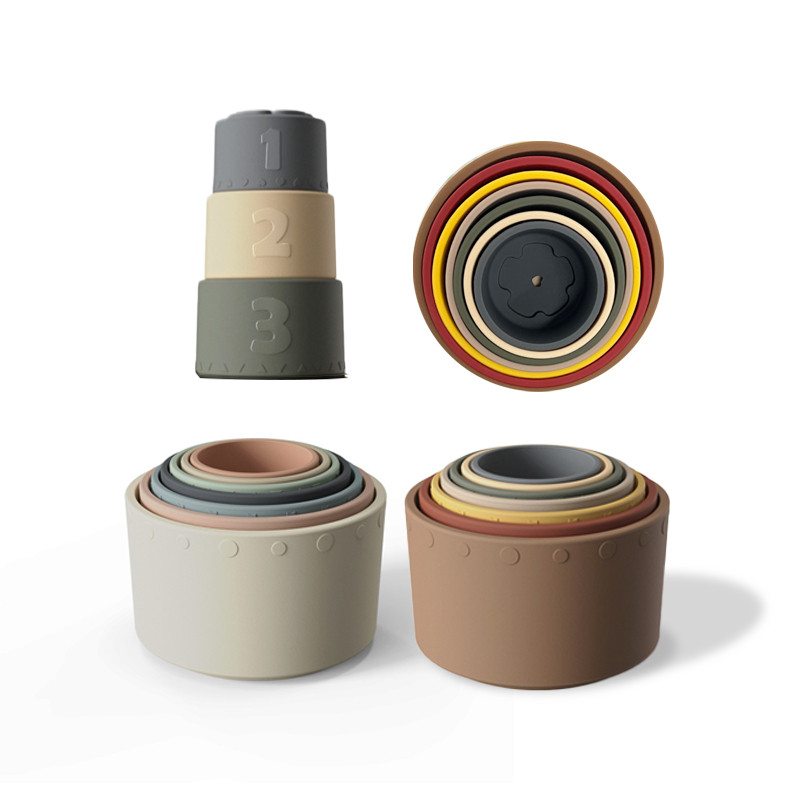