What is the best process for combining silicone molding with metal?
Silicone custom processing
The optimal process for combining silicone molding with metal depends on various factors, including the specific requirements of the product, production environment, cost budget, and the technical level of the factory. The following are some common processes and characteristics of silicone molding and metal bonding:
1、 Liquid Silicone Injection Molding (LSR Injection Molding)
Process description: Liquid silicone injection molding is a process of injecting liquid silicone material into a mold to wrap metal parts.
advantage:
High precision: It can achieve high-precision bonding between silicone and metal.
High degree of automation: suitable for large-scale production, improving production efficiency.
Strong adhesion: By appropriate surface treatment and injection parameter control, it is possible to achieve a strong adhesion between silicone and metal.
Key steps:
Pre treatment of metal components: cleaning, polishing, sandblasting, chemical treatment, etc.
Mold design: Design molds suitable for liquid silicone injection molding.
Injection molding: Control the injection speed, pressure, and temperature to ensure that the silicone evenly covers the metal surface.
Curing: Control the curing temperature and time to ensure that the silicone is completely cured.
2、 Hot vulcanization molding
Process description: Hot vulcanization molding is a process of vulcanizing silicone materials at high temperatures to bond them with metal components.
advantage:
High strength bonding: Through high-temperature vulcanization, the bonding strength between silicone and metal is high.
Good high temperature resistance: suitable for products that require high temperature resistance.
Key steps:
Pre treatment of metal components: cleaning, polishing, sandblasting, chemical treatment, etc.
Preparation of silicone material: Select silicone material suitable for hot vulcanization.
Mold design: Design molds suitable for hot vulcanization molding.
Sulfurization process control: Control the vulcanization temperature and time to ensure complete vulcanization of silicone gel.
3、 Cold vulcanization molding
Process description: Cold vulcanization molding is a process that combines silicone gel with metal through chemical reactions at room temperature.
advantage:
No need for high temperature: suitable for temperature sensitive metal materials.
Easy to operate: The process is relatively simple and suitable for small-scale production.
Key steps:
Pre treatment of metal components: cleaning, polishing, sandblasting, chemical treatment, etc.
Preparation of silicone material: Select silicone material suitable for cold vulcanization.
Chemical reaction control: Control the chemical reaction conditions to ensure a strong bond between silicone and metal.
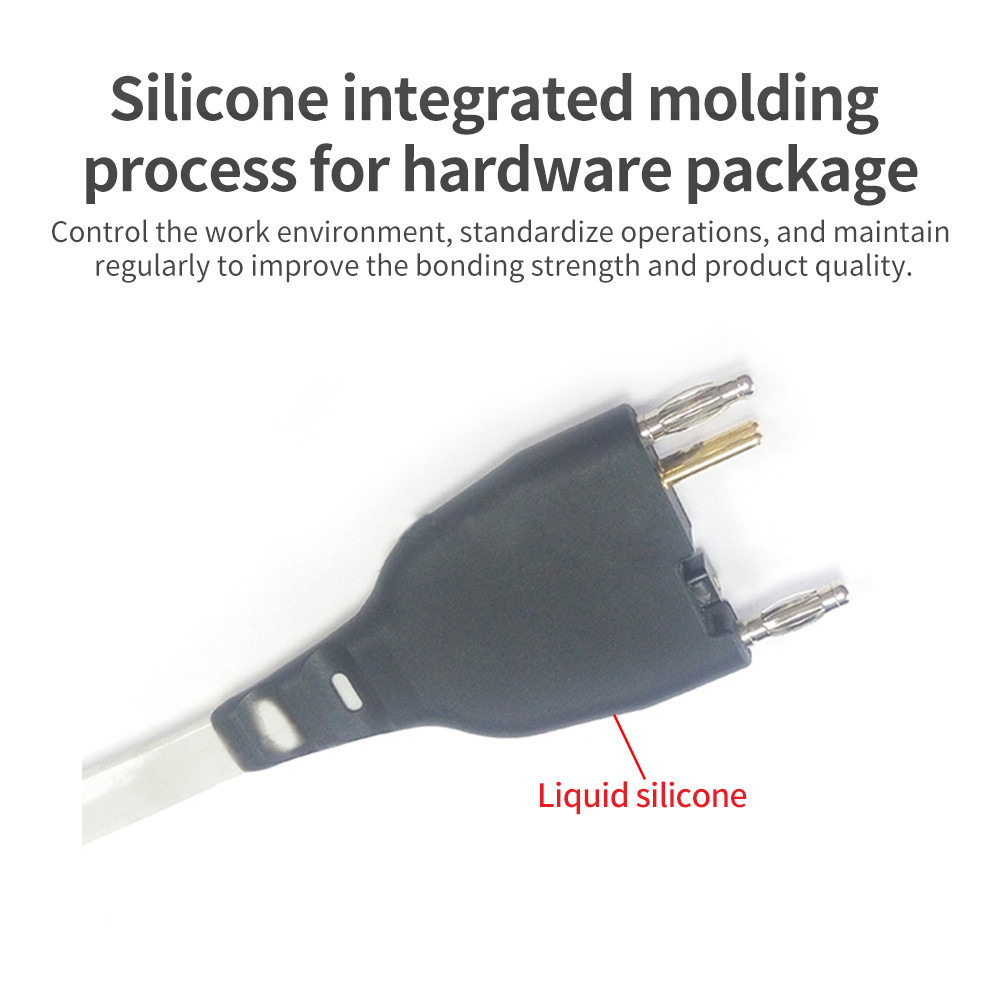
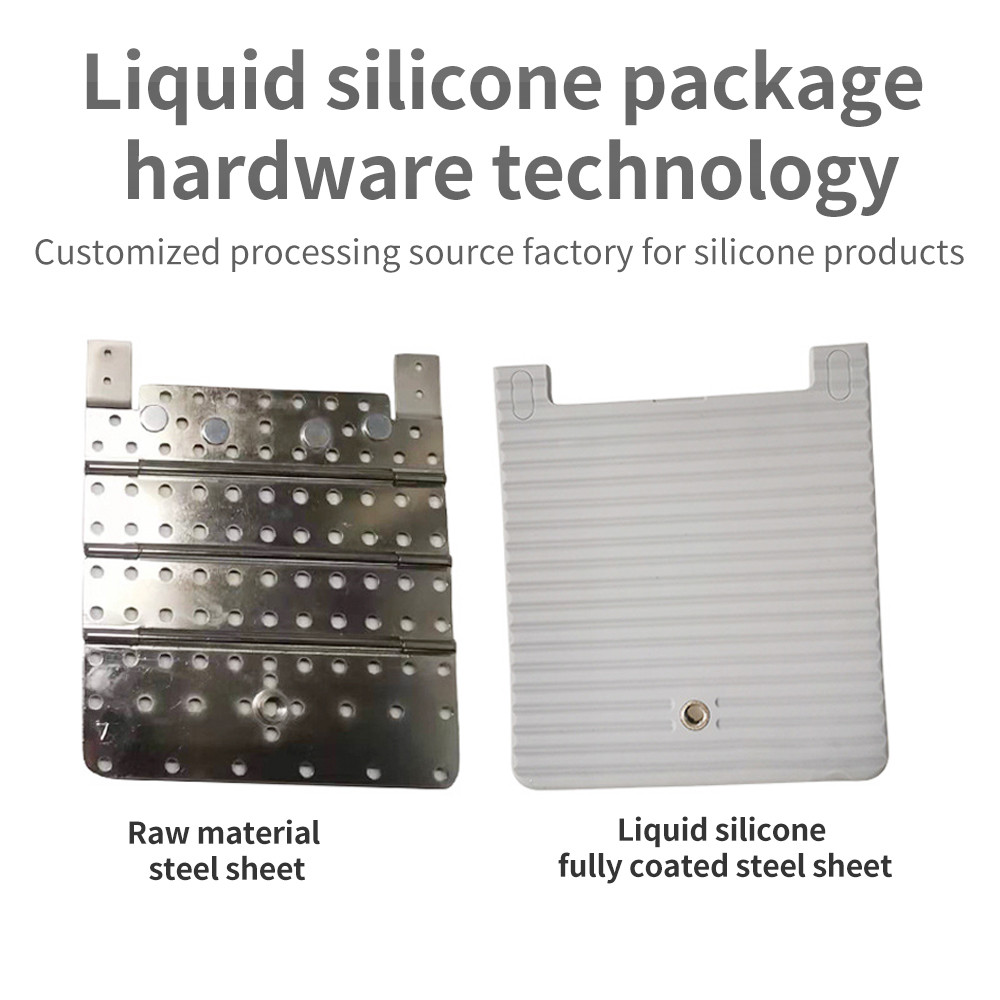
4、 Secondary molding
Process description: Secondary molding is a process of injecting metal parts first, and then injecting silicone on top of them.
advantage:
Complex structure implementation: suitable for producing products with complex structures.
Firm adhesion: Through two injection molding processes, ensure a strong bond between silicone and metal.
Key steps:
Pre treatment of metal components: cleaning, polishing, sandblasting, chemical treatment, etc.
First injection molding: Injection molding of metal parts.
Second injection molding: Inject silicone onto metal components to ensure even coverage of the metal surface.